一方、お客様から添加剤とは何か?その役割、有用性のご質問をお受けすることも多く、BYK社提供の文献をもとにコーティング用添加剤の物理、化学的基礎をWEB連載にてご紹介いたします。
コーティング用添加剤 少量の添加で ‒ 大きな効果
湿潤剤
樹脂溶液の顔料アグロメレートへの濡れには、多くの因子が関係する。アグロメレートへの溶液の進入速度は、粒子の表面特性・表面状態、溶液の粘度、アグロメレート構造の空のスペース配列等に依存する。「湿潤剤」は、液相の表面張力を低下させて溶液のアグロメレートへの進入を増加し、濡れを促進する添加剤として定義することができる。この添加剤の特徴は、その表面活性構造にあり、高極性の親水性構造と非極性の疎水性の構造上の成分が、一分子内に一体化している。まさにこの構造により、界面活性を発現し濡れを良くすることができる。
分散剤
分散剤は顔料表面に吸着したあと、電気的反発と立体障害により、顔料表層にあるスペースを保持し、凝集することを抑制することができる。
電気的反発
一般に溶液中の粒子(塗料の顔料)は帯電している。添加剤により、その電荷を強めたり、電荷をコントロールすることが可能である。同じ極性の電荷により、すべての粒子間で反
発力を生じ、凝集が避けられる。対イオンが顔料表面付近に集まり (液相)、電気二重層を形成する(図 5 参照)。二重層の厚さにより安定性が増加する。
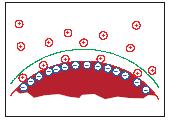
この安定化メカニズムは、特に、水性エマルジョン、水系と高極性溶剤系で有効である。この添加剤は化学的には高分子電解質であり、側鎖に多数の電荷を含む。多くのカルボン酸誘導体が、塗料用の高分子電解質として活用されている。高分子電解質は、顔料表面に吸着した結果、顔料粒子に電荷が移動する。電気反発力は、顔料が一様に荷電されることにより生ずる。これにより、凝集傾向は劇的に減少し、系は安定化する。この添加剤は構造的に湿潤性を示さないので、湿潤剤との併用が必要となる場合がある。
立体障害
立体障害をもたらす分散剤には、二つの特別な構造上の特性がある (図 6 参照)。第一に、
顔料表面に強力に、かつ永続的に吸着する顔料親和性基(顔料吸着基)。第二に、顔料
表面に吸着後、顔料表面から樹脂溶液中に可能な範囲まで伸びる樹脂相溶性鎖。この構造
により、顔料粒子を効果的に保護することができる (図 7 参照)。
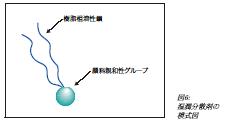
粒子を囲む保護層が拡大する形で添加剤の相溶性鎖と基体樹脂ポリマーとの相互作用に
よって、さらなる顔料安定化が図られる。この安定化メカニズムは、溶剤型と水系のシステムで有効である。顔料親和性基(高極性)と樹脂相溶性鎖(低極性)をもつので、これらの添加剤は優れた界面活性を示し、凝集を防ぐだけでなく湿潤剤の機能も有する。
好みの色合いを実現するためにほとんどの着色塗料には複数の着色材が含まれている。色
浮きと色分れは、異なる顔料が分離して、塗料中で顔料が不均一に局在化する現象である。
もし、塗料表面で顔料濃度に差がある場合を、色分れという。表面は均一な色には見えず、典型的なセル構造が見られる (図 8 参照)。一方、それらの濃度差が塗料表面水平方向でなく、縦方向に起こる場合は、色浮きと呼ばれる。この場合、塗膜表層は均一の色に見えるが、たとえばラビング試験をした場合などで観測される (図 9 参照)。
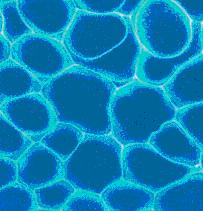
不完全な顔料安定性と顔料易動度の差が色浮き・色分れの原因である。液体の塗膜は塗布後、非常に動的である。溶剤が蒸発し、物質はウエット塗膜の下から上へ、そしてまた下へと動く。これらの傾向は、六角形セル構造で、ベナードセルとして知られている (図 10 参照)。顔料は、濃度差と粒子サイズ差により易動度が異なるとき分離が発生し、その結果、色浮き・色分れを起こす。
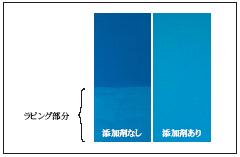
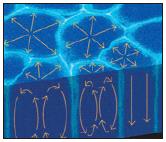
この異なる易動度は、適当な湿潤・分散剤を使うことで調整することができる。樹脂溶液と吸着するポリマーの添加剤が相互作用で顔料粒子の凝集を防止し、樹脂系に組み込まれる。したがって、流動性は粒子サイズと濃度によっては影響されなくなる。それと対照的に、大きなファクターは相互作用である。添加剤によって、全ての顔料の完全な安定化をすることで、色浮きと色分れを改善できる。
湿潤分散剤のタイプコントロールされた凝集湿潤分散剤
顔料吸着基を添加剤分子中のある限定された場所に集中させず、分子中に特別な方法で分布させると、添加剤は多様な顔料粒子を 3次元のネットワーク構造から橋かけとして作用させることができる。この構造は、「コントロールされた凝集」と称する。そして、添加剤は、コントロール凝集タイプの添加剤と呼ばれる。ネットワーク構造には凝集との共通点がいくつかある。重要な違いもあり、それは添加剤なしの場合には、顔料粒子は直接に接触し、コントロールされていない凝集になる点である。対照的に、コントロールされた凝集は、顔料-顔料が接触せず、添加剤は、いつも顔料粒子の間にある。そのサイズと安定は添加量によって決まる。詳細は、添加剤-添加剤と添加剤-顔料の相互作用による。凝集がコントロールされていない状態は常に好ましくないが、コントロールされた凝集はある目的に使用すれば塗装系に好ましい効果をもたらすことができる。コントロールされた凝集状態では、三次元の構造が、擬塑性またはチクソ性を有する。これらの構造は、せん断力で壊れ、せん断力がなくなると復元する。レオロジーの作用は、沈降とタレに影響を与える (詳細はレオロジー添加剤 で別述)。コントロールされた凝集は、光沢の減少等、好ましくない効果の場合もある。好ましくない効果については、ケースバイケースで系を評価すべきである。適正量でコントロールされた凝集タイプの添加剤 (図 11 左参照) はプライマー、下塗り、防食塗料に使える。脱凝集タイプ添加剤 (図 11右参照) については以降の章で説明するが、表面状態、高光沢、レベリングを求めるトップコートに推奨される。
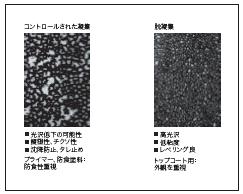
脱凝集タイプの湿潤分散剤
脱凝集によって顔料粒子は小さくなり、低塗料粘度で、ニュートニアン流動作用が起こる。フローとレベリングは良くなり、高顔料濃度化も可能である。脱凝集で小さな粒子サイズは、高光沢を得られ、着色力は向上する。同様に、透明性や隠蔽性も良くなる。
脱凝集することで、効果的に顔料を利用することができ、特に高級顔料を使用するケース場合に経済面でも重要である。
溶剤型塗料用低分子タイプの湿潤分散剤
従来の脱凝集添加剤の構造については前述のとおりである (前述図 6 参照)。
顔料親和性基と樹脂状の側鎖構造からなる添加剤は、低分子量ポリマーで、顔料表面に吸着し、立体障害によって安定化する。これらの湿潤分散剤は、脂肪酸がベースで、長年塗料に使われており、無機顔料やエクステンダーを非常にうまく安定化させることができる。有機顔料使用量増加による高性能化のために、効果的な湿潤分散剤の開発が必要になった。
溶剤型塗料用高分子タイプの湿潤分散剤
添加剤効果において、耐久的不変に顔料表面への吸着は最も重要である。顔料粒子の表面性質は、添加剤の効果に重要である。無機顔料は、高極性の表面で、比較的容易に添加剤が吸着する。それに対して、有機顔料は低極性であり、従来の添加剤では表面への吸着は困難である。
したがって有機顔料を脱凝集・安定化は不十分となる。まさにこのことにより、高分子量タイプの湿潤分散剤が開発された。従来の低分子量タイプに比べ、より多くの顔料親和性基を含んでいる (図 12 参照)。この高分子タイプの添加剤は樹脂に似た性質を示す。なぜなら、構造的特長の添加剤は、強い吸着層を持っている。よって、多くの有機顔料に、耐久的に吸着できる。溶剤ポリマー側鎖は、立体障害で安定化する。
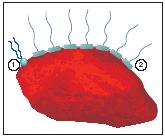
従来の添加剤のようにポリマー側鎖は、樹脂溶剤と良く相性し、適切に広がった時、安定化する。もし、この相溶性が阻害されると、ポリマー側鎖は縮んでしまう。その結果、すべて立体障害と安定化を失うことになる。高分子ポリマー添加剤と多様な塗料樹脂の相溶性は、低分子量よりも、かなり制限されている。従って、化学的に関連がある添加剤は、(分子量、極性、相溶性により区別)使用できる。高分子ポリマーの推奨添加量は、従来の低分子量よりもかなり高い。高分子ポリマーの湿潤分散剤は、有機顔料用に開発されたが、擬塑性無機顔料にも同様に使用できる。
使用方法
添加量
適した湿潤分散剤の添加量は、他の添加剤同様に、最も重要である。添加剤は顔料表面に付くように設計されるため、必要な添加量は顔料表面の面積に依存する。従来の湿潤・分散剤は、低分子ポリマーがベースで、無機顔料で0.5-2%、有機顔料で1-5%使用すること(顔料重量比)。高分子量添加剤の添加量は、かなり高い。特に、小粒子サイズの有機顔料には必要になる。添加量が多いのは、顔料表面積が大きいためである。ポリマー添加剤は、樹脂のような性質を有し、塗膜の耐久性に影響を与えない。フロリダの屋外暴露テストとウェザー機器で両方とも10年以上の耐久性が確認された。一般的な添加量は、無機顔料用で1-10%、有機顔料用は 10-30% である。とても微細な粒子顔料 (例えばカーボンブラック) は、60-80% の添加量が必要である。適した安定化の目安として、光沢と透明性を測定し、顔料混合の作用の色浮き、色分れはラビング試験で評価する。
添加のポイント
湿潤分散剤は、最適な効果を生むためには、ミルベースの分散時に添加しなければならない。理論上では、なによりもまず顔料、溶剤、添加剤のみを混合 (予備混合) した場合に最適な効果が得られる。こうすることで、樹脂ポリマーと競合せずに添加剤を顔料へ吸着できる。しかし、実際にこの方法が必要なのは最悪な事態を想定した場合だけである。添加剤を後添加することが求められる場合や製造終了後、色浮き、色分れ、凝集問題を解決するために添加される場合もある。これらに、いくつかの添加剤は適しており、その場合、高添加量が必要になる。
ピグメントコンセントレート
ピグメントコンセントレート (顔料ペースト) は塗料業界で広く活用されている。それらは、着色、調色ベース、フルミキシング (インターミックス)に使用される。適切に顔料を安定化させ、ハンドリングを容易にする湿潤分散剤は、代用の効かない成分である (図 13 参照)。
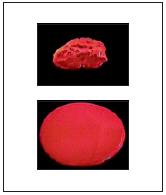
レオロジーコントロール剤との併用
記載したように、コントロールされた凝集分散剤は、塗料のレオロジーに影響を与える。本来、レオロジーコントロールは、他のレオロジーコントロール剤(焼成シリカ、ベントナイト、脱水剤、ひまし油) と一緒に使われ、相乗効果が得られる。オルガノクレー (ベントナイト) は、一般にペーストで添加される。ここで湿潤分散剤は、ペーストの製造を最適化することができる。
湿潤分散剤の副効果
二つの主要な理由で、湿潤分散剤は使われる。一つ目は、顔料の濡れ。二つ目は、顔料分散の安定化である。添加剤は、塗料性質に影響を与える。例えば、レオロジー効果(沈降とタレ防止)は、先に述べた。重要なのは、レオロジー性質が変わると、フロー特性も泡にも影響を与える。脱凝集湿潤分散剤は、フローとレベリング剤として働き、泡の生成防止、消泡を推進する。湿潤分散剤の選定が適切でないと、塗膜性能に障害がでて、防食性が減少する。添加剤が適切だと、防食性が良くなる (図 14参照)。
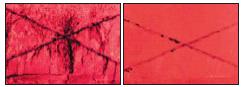
湿潤分散剤を選定した時、二つの重要なファクターを、同時によく考えなくてはならない。一つ目の因子は、もちろん添加剤の湿潤分散性への影響。二つ目は、添加剤の塗料に対する総合的な影響についてである。
BYK社(ドイツ BYK-Chemie GmbH, Dr. Wilfried Scholz 著)提供の"Coating Additives"をベースにビックケミー・ジャパン株式会社が翻訳・監修いたしました。
日本語訳総監修 ビックケミー・ジャパン株式会社 若原 章博
翻訳 同社 日野 真司 樋口 公志 横手 涼 菊池 雄 神代 智史
BYK company profile:
BYKは塗料、インキおよびプラスチック業界で使用される添加剤では、世界的なリーディングサプライヤーの一つです。添加剤は塗料、インキおよびプラスチックの製造工程で使用され、製造工程を最適化し、最終製品の品質、外観を大きく向上させます。BYKでは、湿潤分散剤、スリップ性、レベリング性を向上させる表面調整剤、消泡剤、レオロジーコントロール剤をはじめ、
ナノテクノロジーを応用した添加剤、ワックス添加剤等を取り扱っています。